Within today’s fast-paced manufacturing landscape, the pressure to innovate and bring products to market quickly has never been greater. Companies are constantly seeking methods to streamline their production processes while maintaining high quality and cost-effectiveness. This is where rapid injection molding emerges as a game-changing solution, providing a pathway to not just efficiency but also a significant competitive advantage. By leveraging advanced technologies and optimized workflows, manufacturers can minimize lead times and respond swiftly to market demands.
Rapid injection molding revolutionizes the traditional injection molding process, allowing for the rapid creation of prototypes and production-ready parts in a small portion of the time. This method addresses the challenges of long development cycles and high tooling costs, empowering businesses to test ideas, make necessary adjustments, and launch products with unprecedented agility. As a result, companies that embrace this innovative method find themselves not just keeping pace with industry trends and setting new standards in product development and delivery.
Comprehending Quick Injection Moulding
Quick injection moulding is a breakthrough in the world of product manufacturing, enabling companies to produce plastic parts quickly and effectively. This method makes use of advanced methods and substances to fabricate molds faster than traditional methods. As a consequence, producers can substantially reduce lead times and improve product launch timelines for new products, which is essential in the current challenging landscape.
The technique depends on computer-aided design and three-dimensional printing to produce models and molds that allow the injection of molten plastic into them. This permits the rapid production of both tests and final parts, allowing designers and engineers to modify designs and test them without the prolonged wait linked to conventional molding techniques. The flexibility provided by rapid injecting molding not only improves innovation but also streamlines the design procedure.
In addition to quickness, quick injecting moulding can also result in financial efficiencies. By cutting the time spent on tooling and mold production, companies can distribute resources efficiently and minimize waste. Furthermore, the capacity to create little to moderate production runs without the overhead costs typically connected to conventional manufacturing techniques makes this method an enticing option for businesses looking to gain a business edge in their respective industries.
Advantages of Rapid Injection Processing
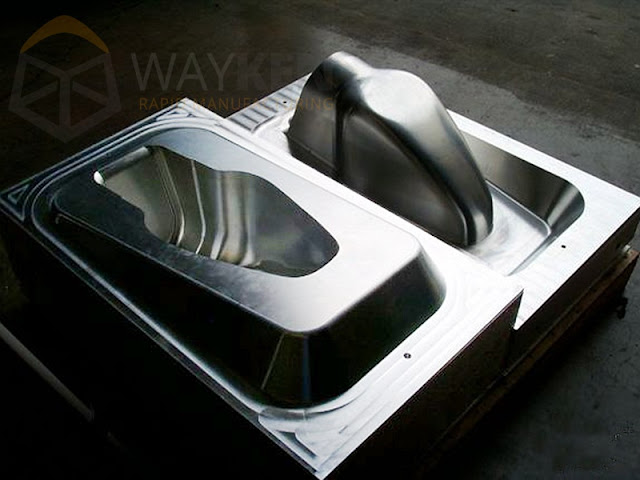
Rapid injection molding offers various advantages that substantially enhance the fabrication process. One of the most notable advantages is the cut in time-to-completion for item development. Traditional injection molding can take days to set up, but speedy injection molding streamlines this process by utilizing cutting-edge technologies and materials. This allows manufacturers to bring their goods to market more rapidly, giving them a competitive edge in industries where time-to-market is critical.
Cost-effectiveness is another important benefit of accelerated injection molding. By allowing for smaller production runs and using less expensive materials for test models, companies can try out with designs and modifications without facing major financial risks. This adaptability not only reduces upfront investment costs but also allows manufacturers to improve their products based on consumer input before investing to bigger production volumes.
Lastly, accelerated injection molding promotes new ideas by facilitating design iterations. With the ability to swiftly produce and test several prototypes, teams can investigate different design possibilities and perfect products for performance and design. This cyclical approach fosters a culture of originality and responsiveness, ultimately leading to improved end products that meet customer needs and preferences.
Implementing Accelerated Injectable Molding Strategies
To effectively implement rapid injection forming strategies, organizations need to start by re-evaluating their design and prototyping processes. Employing advanced CAD programs can significantly enhance the design phase, enabling teams to create and alter complex shapes with simplicity. Timely detection of design errors becomes critical, as accelerated injection forming is extremely responsive to dimensional precision. By integrating simulation software, manufacturers can foresee potential issues in the forming process and optimize designs before manufacturing starts, minimizing the time to market for new offerings.
Next, cooperation between multidisciplinary teams is necessary for optimizing the advantages of accelerated injection molding. Technical staff, designers, and manufacturing specialists should work closely from the beginning to ensure that all perspectives are taken into account. Implementing an agile approach can enhance communication and decision-making, aiding to quickly adapt to market needs and responses. This integrated method promotes a culture of creativity, which is essential for identifying new uses and enhancing existing practices in rapid injectable molding.
Ultimately, investing in the latest technology and tools is a game-changer for effective implementation. High-performance injection molding machines, alongside cutting-edge materials, can boost productivity and reduce cycle durations. Additionally, incorporating automation and IoT capabilities can further enhance manufacturing monitoring and quality assurance. By remaining at the leading edge of tech innovation, organizations can guarantee they stay competitive in the constantly changing landscape of goods manufacturing, making rapid injectable molding a central foundation of their strategy.